the vision
A high pressure pump unit designed specifically for net cleaning applications. The unit needed to be capable of operating for sustained periods in harsh, marine environments. Reliability, long service intervals, and low overall cost of ownership were critical factors to slash the running costs incurred by existing pump units.
the solution
To achieve the right result, rather than adapt our existing product, we designed from the ground up. Our starting point was to work closely with the end client to better understand their application, the environment and the operational challenges. That said, much of the technology was taken from our market-leading MultiJet range. Our MultiJet pump units have been developed over more than two decades and operate reliably in many applications and industries around the globe.
The base frame was designed specifically for this unit, with both fork-lift slots and lifting eyes for movement by fork-lift truck during dockside handling or by the on board vessel or crane. An important feature is that the base frame is used to store the fuel, thus giving a low centre of gravity and increasing unit stability. With no requirement for a separate fuel tank, there is both a significant space and weight saving.
Reliability is important for all industries, and this is especially so for marine aquaculture. With the remote nature of these operations, unit breakdowns can be particularly troublesome and costly. We utilise the Hammelmann reciprocating plunger pump in our MultiJet units and have done so for many years. We have found the Hammelmann pump, with its packing-free plunger sealing solutions to be the most reliable, low maintenance, and cost-effective pump for high pressure applications. This high pressure plunger sealing reliability, coupled with the long service intervals, provides a low cost of ownership throughout the operational life of the unit.
The application-specific features incorporated into this unit include:
- Adjustable pressure – simple manual pressure adjustment within predefined limits to suit the application/cleaning performance requirements.
- Seawater lift pump – to deliver seawater directly from the ocean to feed the high pressure pump.
- Material selection/coating – to protect against the salt-rich environment the components are manufactured from stainless steel, or coated with a high quality, marine specification paint system.
- Winch – mounted inside the unit, this hydraulically driven, variable speed winch allows the net cleaning head/ROV to be lowered and raised at a controlled rate. A fuel-saving feature is that the winch is powered from the unit’s own engine so there is no need for the vessel’s auxiliary power to be running. Standard winch controls are mounted to the unit and there is an option for remotely controlled winch operation.
The environmental enclosure is a common feature of our units built for outdoor operation. It has the following functions:
- Protects the equipment from the elements.
- Protects the equipment during transport.
- Provides a natural noise attenuation barrier and has options for further noise attenuation enhancements.
- Houses the control panel allowing the operator to control the unit from outside.
- Lockable doors allow the safe storage of hoses and ancillary equipment.
The system control panel was programmed to suit the extra winch equipment required and a facility was included that allows the operator to monitor the machine via an Ethernet link.
the result
The customer received a high pressure pump unit which was not only designed to suit their exact requirements, but that was capable of a variety of tasks. Such has been the reliability of this unit, the customer returned on a number of occasions to purchase more Calder net cleaning units for their global operations
Visit our net cleaning page.
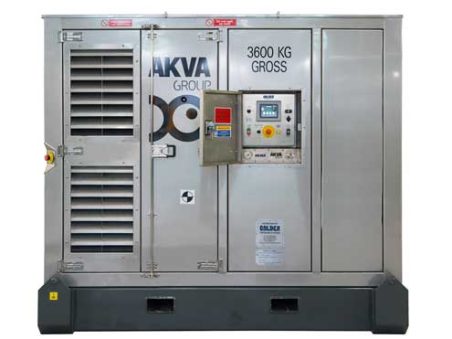
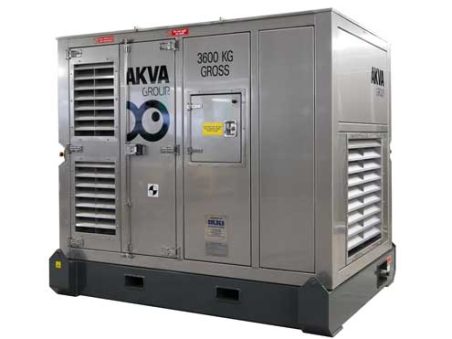
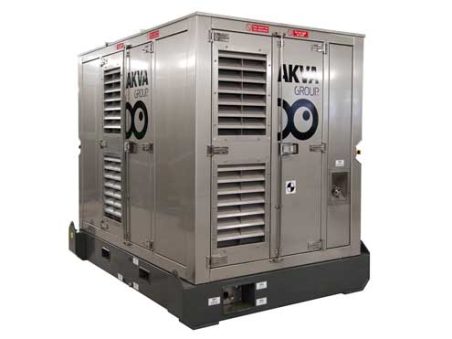
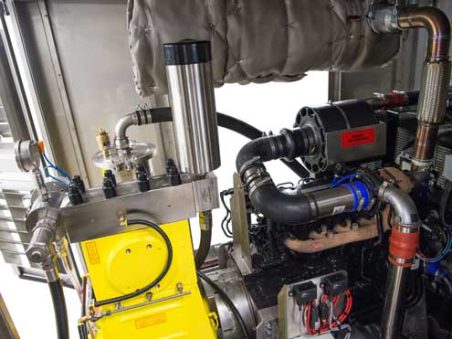
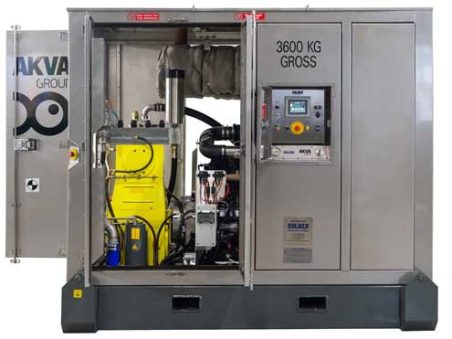
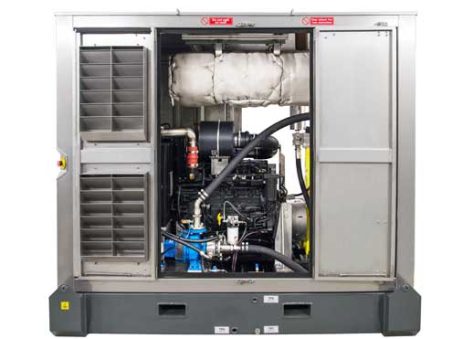
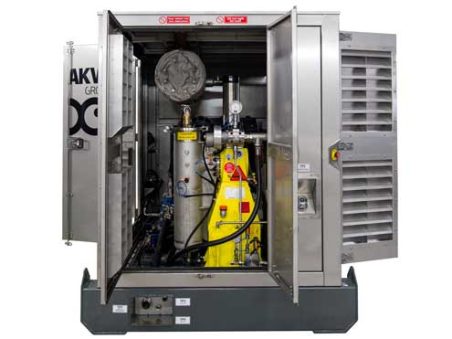
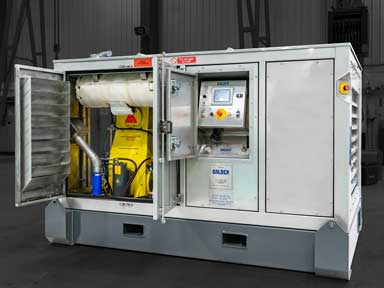