HPHT Wash Water Skids
A leading Aberdeen company ordered two wash water pump packages for operation in a HPHT (high-pressure/high-temperature) offshore location. These pump skids have gone through our engineering and design process, and are now well into the build process in the workshop.
HPHT Wash Water Skids – build progressing well
Starting with the base frame, build started. We fitted and aligned the pump and motor. Then each unit received its spherical resonator and we used 3D design to ensure the pipe spools were a perfect fit. The mechanical team are finishing off and the electrical team are gearing up for their work.
Once complete, we shall wheel the units into the test bay for thorough F.A.T. testing. Lastly, we will conduct pre-delivery inspections before despatch.
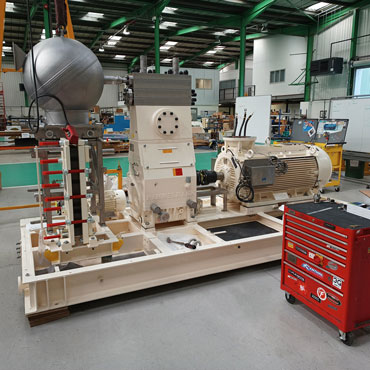
Baseframe – Fabrication, Painting and Arrival
Projects often feel like they are really coming alive when the baseframe is complete and assembly begins. As is typical for our process pump skids, these baseframes have been subject to strict weld procedures, non-destructive examination procedures and load testing. The design underwent FEA analysis to ensure structural integrity. However, we back up this analysis using traditional methods. Following fabrication and painting, they arrived on the shop floor.
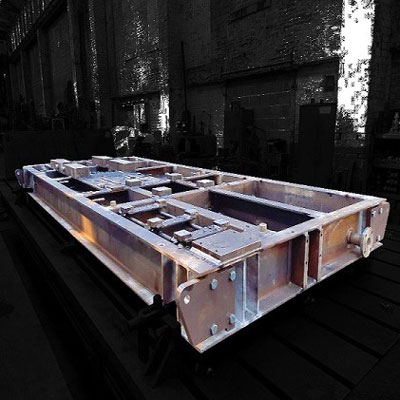
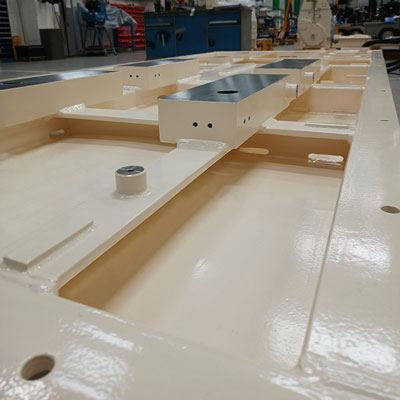
The Pumps Arrive

This Hammelmann HDP 400 series unit will pump over 200 litres per minute of seawater at a pressure above 600 bar. Powering the pump will be a fixed-speed, fan-cooled electric motor.
Coupling Alignment
Coupling manufacturers recommend maximum tolerances on alignment of rotating equipment. However, we typically work to less than half the recommended tolerance. In order to achieve these greater levels of accuracy, we use the latest laser alignment equipment. This, coupled with the experience our build teams possess, ensures we achieve our stringent pump/motor alignment requirements.
For most of our pump packages, we use shaft-to-shaft couplings. This eliminates the side loads frequently experienced with belt drives. We generally opt for a flexible membrane coupling as shown in the picture.
One advantage of flexible membrane couplings is the enhanced reliability they offer. Another huge advantage they have over other coupling designs is their easy separation for commissioning and maintenance. The coupling has a central spacer. During maintenance, this spacer is removed allowing rotation of the pump and/or motor without disturbing their alignment. Thus, on re-assembly, no re-alignment is necessary.
The couplings we use adhere to international standards. Manufacture of the coupling on this pump skid is to the enhanced requirements of API 671. It is also ATEX compliant.
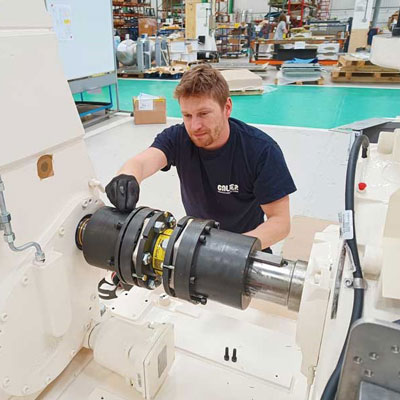
Why do we Use Resonators?
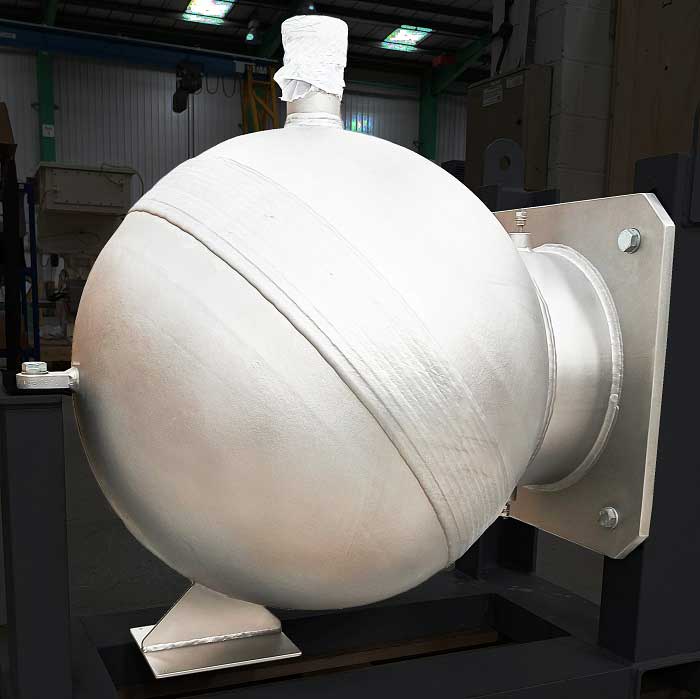
Resonators minimise pressure pulsations and we use them on the suction and discharge lines. The spherical design has two significant advantages over traditional bladder type dampers. Firstly, they are maintenance free. Secondly, they require no pre-charge. Significantly, this means they can operate across the unit’s full operating pressure range without need for adjustment. We check the resonator design using Finite Element Analysis to ensure the resonator meets our customer’s requirements in relation to torsional analysis, explosion-related blast cases, and seismic loads.
3D Scanning of Pump Skids
We had full 3D scans created of each unit. This allowed the pipe spools to be fabricated right first time. There are many uses for 3D scanning of pump skids. With our experience of designing pump packages for space- and access-limited locations on offshore platforms and FPSOs, having an accurate 3D scan is a useful option.
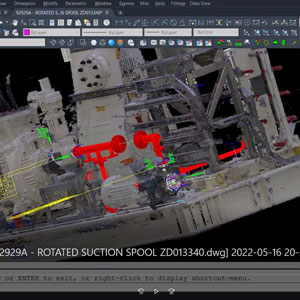

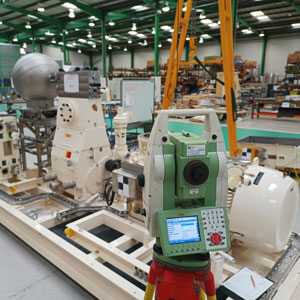
More about these HPHT Wash Water Pump Skids
The process pipework is Duplex stainless steel. We fit a suction damper (fitted with skid-edge charging point and gas side safety valve) and resonator to achieve the required pulsation limits. The lube oil system includes twin independent lube oil pumps, twin oil filters, and plate heat exchanger. Included in the package is a temperature control valve for low temperature starting.
The units will also feature a vibration monitoring system, pump crosshead temperature monitoring, motor bearing temperature monitoring, suction pressure transmitter, lube oil temperature and pressure transmitters, and a fire and gas detection system. These liquid injection pump units will be skid mounted and will have a stainless steel environmental, acoustic enclosure.
The platform has space restrictions from lay-down point to final position. The design is, therefore, modular to allow site movement and final position re-assembly.
Get in Touch
We are here to help. Please call to discuss how we can help with your pumping applications on +44 1905 751790 or email sales@calder.co.uk.
Alternatively, learn more about our pump packages for the energy sector.